The final installment of the Off-Campus Project report series features their visit to the SUBARU Visitor Center and Yajima Plant in Gunma. Cameron Ralph and Ayoob Iliyas, 3rd GSEP students from the UK and India, share their experiences:
“The visit to the Subaru Yajima Plant allowed us to tour the production line for the Forester and Legacy Model of Subaru, as well as the visitor centre containing some of their historic cars. Unfortunately photos were not allowed inside the production plant so we will have to do our best to describe it.
The production plant has been heavily automated, with many machines shaping the body of the car, as well conducting the welding on metal parts such as the doors. However, they still maintain the traditional human based assembly line. This assembly line consisted of 130 stations, where all components of the car are attached, such as fixing the chassis to the body of the car, all the way to the end where they pumped hydraulic brake fluid through the car. One thing that I think caught everybody’s attention was that if one part of the line was falling behind or causing any problems, they would play a specific song to notify the section leaders of the need for asssitance. (The line would be stopped if they still could not fix the problems.)
After the car was constructed, you could see in the plant they had a small testing area for tyre and steering wheel angle adjustments, initial EyeSight and audio settings. A lot of the material testing and quality control is automated by machines during production stages. This means most components are individually tested, alongside the final product. (The final inspections are carried out in a next-door dedicated final inspection building. ) However, major components such as the gearbox and engine are manufactured at Ohizumi plant and transported there.
I think one thing that really surprised me was the sheer scale and speed that the production of the cars moved at. Initially I thought the manufacturing of a car would be quite a slow and intricate process, but automated robots and an efficient assembly line means that the Main and Yajima and plants could produce up to 2,500 units daily when operating at full capacity. When installing heavy parts (e.g. engines, glass, sunroofs, seats, mufflers), assistive equipments are used to alleviate the load on the operators. Earplugs are also used for loud processes to protect ears.
The logistics behind the operation is quite extraordinary. There are around 30,000 parts in a car and at Subaru, they source it from 260 companies and suppliers. These then undergo multiple stages before we get the finished product. We start with the raw materials undergoing the stamping process, where sheets and rolls made into the starting template design. The next process is Body Welding Assembly Process, which takes around 4 hours. The templates are modified to the desired shape and then welded together. Then it is in White Body Storage (WBS), which is the stage between the welding and painting process. It is transported by conveyor belt and takes an hour.
Up next is the painting process, where the painting is done. Multiple layers are done and this takes 8 hours. The next 1 hour is spent in Paint Body Storage (PBS), which is the time on the conveyor from the painting area to the assembly area. In the final assembly, the engine and other parts are placed. This goes on for 4.5 hours. The last process is the final inspection, which lasts 2.5 hours (including waiting time for inspection) and various tests are done on the car before it is shipped to an outlet. All in all the entire process comes out to 21 hours and this doesn’t even include the pressing and stamping.
The entire experience was both to our expectations and not to our expectations. Different aspects played to our image of how manufacturing plants are, like the process and how the line is but then other aspects were so different, like how the automation and humans work together, the parts being sources and so on. In the conclusion, we were shown around the centre and how ‘The Subaru Eyesight’ works and assists drivers. Photographs weren’t allowed inside, so the best we can do is pictures of the visitors centre and the cars being exhibited.”
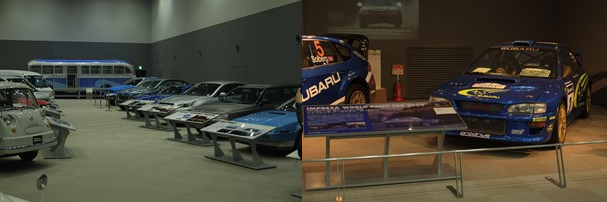

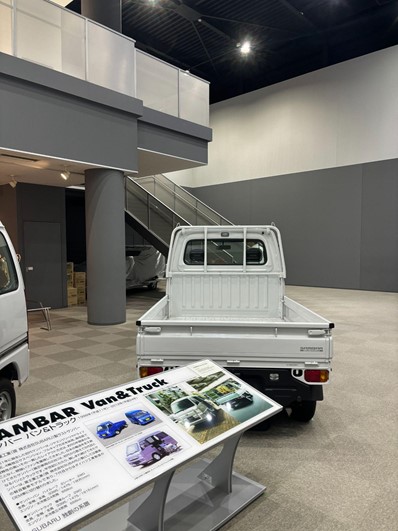